In the servo system, a compensation device (usually a compensation circuit) with linear characteristics is commonly used, which adopts series, feedback (or parallel), negative feedback, positive feedback, and a combination thereof to improve the characteristics of the system and improve the system. Quality of work. The following describes the characteristics of various compensation connection forms and related precautions.
Common linear compensation for servo systems1. Series compensation
Series compensation refers to the integration of appropriate compensation devices (circuits) in the main channel of the system (ie, the forward channel). as the picture shows.
The commonly used series compensation devices are composed of circuits, and there are passive compensation networks composed of only R, L, and C. There are active compensation networks composed of linear integrated amplifiers, all of which can transmit DC signals, so only the parts that transmit DC signals in series in the system line can play a corresponding role. If the system transmits a fixed frequency AC carrier signal, the above two types of compensation networks cannot be used.
There are many forms of commonly used compensation networks that are practical in engineering. As a series compensation of the system, some of them cannot be used because in the main channel of the system, circuits with pure differential links cannot be connected in series (ie, networks without zeros with s=0 are not connected in series), which will block the constant The effective transmission of the signal prevents the servo system from working effectively.
In order to improve the steady-state accuracy of the system, it is often adopted to improve the type of the system (ie, no difference), which requires the integration of the integral link in the forward main channel of the system, or the series PI regulator.
In case the system open-loop logarithmic amplitude-frequency characteristic (the system is the minimum phase system), as shown by curve 1 in Figure 5.40a. Under zero initial conditions, the response of the system to the input step signal can meet the dynamic quality requirements, but the steady-state accuracy of the system is not high; to improve the system steady-state accuracy, the system open-loop gain needs to be increased, and the system open-loop logarithmic amplitude frequency The characteristics are shown in curve 2 in Figure a, but the dynamic quality of the system does not meet the requirements. While increasing the system open-loop gain, serially connect a lag compensation
There are many factors affecting the servo system control, the most important of which are servos such as position, speed, acceleration and vibration. The control accuracy of the system is one of the most important technical indicators. The control accuracy of the servo system is affected by many factors. The key to the accuracy of the detection device is resolution. The development of modern science and technology, the use of high-precision servo systems is increasing. For example, the high-precision phase-locked speed control system requires the speed measurement error "i0~, while the general speed measuring generator speed measurement error is 2%. 0.02% range. The radar antenna servo system used to track satellites must have a tracking error of 1'.
Observing celestial radio telescopes requires a servo system error of "0.05'. Beginning to enter the home TV laser player, the radial motion of the laser needle is controlled by the servo system, and the position error of the system is ≤1胛. The above examples show that the accuracy of the servo system is higher, and the accuracy of the detection device they use will be higher. First, the detection device in the system can distinguish the error and provide an effective signal before talking about controlling the system. Therefore, the high precision of the detecting device is a prerequisite for realizing a high-precision servo system. However, servo systems for various purposes are diverse, and their accuracy requirements are also very inconsistent. Because of this, the types of detection devices used in servo systems are very complicated. This section only uses common analog speeds and A simple description of the angle measuring (displacement) device.
1. Angular velocity detection
In the speed servo system, the output of the system must have a device for detecting the angular velocity. In the position servo system, it is also often required to obtain the speed damping signal. Therefore, it is widely used in servo systems. The most used ones are various speed measuring generators. The relatively simple ones have speed measuring bridges. The more accurate ones are incremental code disks.
(1) Speed ​​measuring generator
12V
Dc Motor Can drive under the rated voltage 12 v dc motor, most of the products our company can achieve the 12 v voltage drive, speed can be customized according to customer demand.
Characteristics: 12V dc
motor With torque, low noise, small size, light weight, easy to use, constant speed operation, etc, also can match all kinds of reducer in order to achieve the purpose of changing the output speed and torque
Application field: 12V Dc Motor part of the armature iron core, armature, commutator and other devices, dc motor is suitable for most of the electronic products, such as electric toothbrush, razor, medical apparatus and instruments, breeze machine, mixer, etc
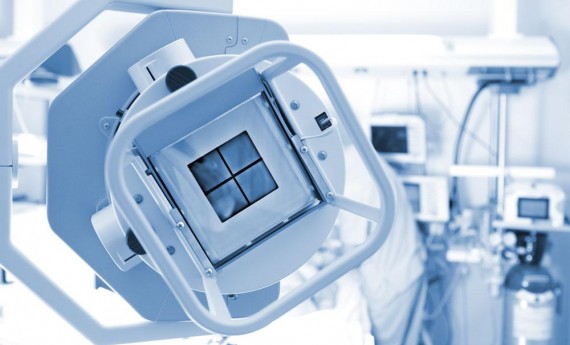
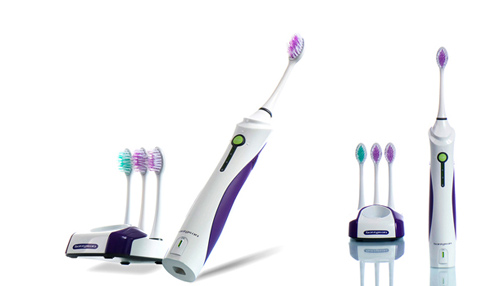
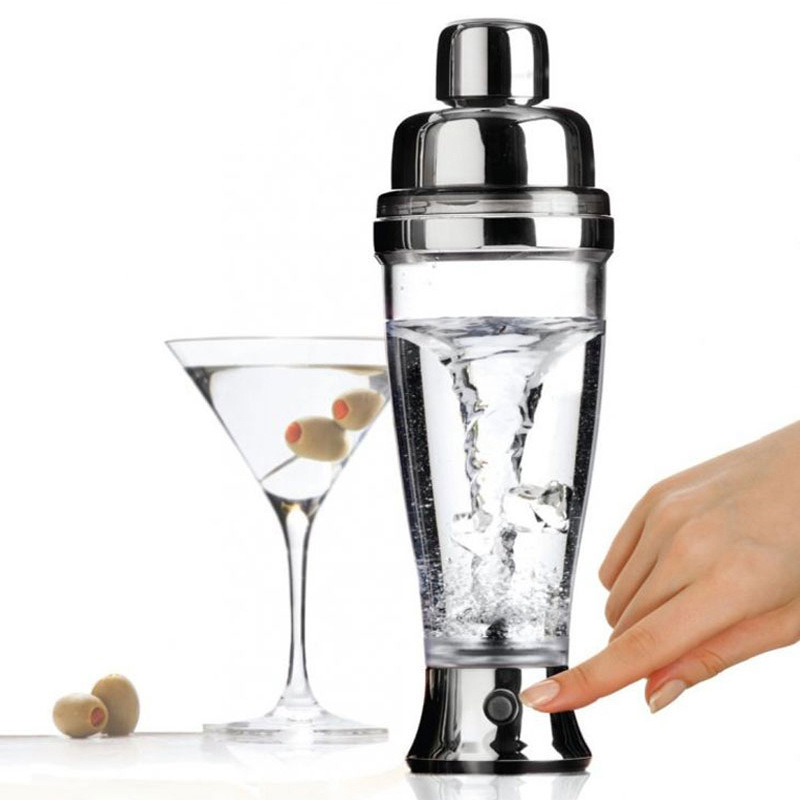
Method of use: the best stable in horizontal plane, installed on the 12V dc motor output shaft parts, cannot use a hammer to knock, knock prone to press into the 12V dc motor drive, may cause damage to internal components, and cannot be used in the case of blocked.
Operating temperature range:
12V dc motor should be used at a temperature of -10~60℃.
The figures stated in the catalog specifications are based on use at ordinary room temperature catalog specifications re based on use at ordinary room temperature (approximately20~25℃.
If a 12V dc motor is used outside the prescribed temperature range,the grease on the gearhead area will become unable to function normally and the motor will become unable to start.Depending on the temperature conditions ,it may be possible to deal with them by changing the grease of the motor's parts.Please feel free to consult with us about this.
Storage temperature range:
12V dc motor should be stored ta a temperature of -15~65℃.
In case of storage outside this range,the grease on the gearhead area will become unable to function normally and the motor will become unable to start.
Service life:
The longevity of geared motors is greatly affected by the load conditions , the mode of operation,the environment of use ,etc.Therefore,it is necessary to check the conditions under which the product will actually be used .The following conditions will have a negative effect on longevity.Please consult with us should any of them apply.
â—Use with a load that exceeds the rated torque
â—Frequent starting
â—Momentary reversals of turning direction
â—Impact loads
â—Long-term continuous operation
â—Forced turning using the output shaft
â—Use in which the permitted overhang load or the permitted thrust load is exceeded
â—A pulse drive ,e.g.,a short break,counter electromotive force,PWM control
â—Use of a voltage that is nonstandard as regards the rated voltage
â—Use outside the prescribed temperature or relative-humidity range,or in a special environment.
â—Please consult with us about these or any other conditions of use that may apply,so that we can be sure that you select the most appropriate model.
when it come to volume production,we're a major player as well .each month,we rurn out 600000 units,all of which are compliant with the rohs directive.Have any questions or special needed, please contact us, we have the engineer group and best sales department to service to you Looking forward to your inquiry. Welcome to our factory.
12V Dc Motor,Dc Motor 12V,12 Volt Dc Motor,Low Rpm Dc Motor
Shenzhen Shunchang Motor Co., LTD. , https://www.scgearmotor.com